Social Impact
We care about every person impacted by our business, including those in our supply chain. We have a Social Compliance Program in place to monitor for slavery and human trafficking activity, among other responsible purchasing practices. A supplier’s failure to meet our requirements will result in corrective action, which may include removing the supplier from our approved vendor list.
Our efforts at preventing forced labor and human trafficking in our supply chain include conducting Social Compliance audits and the associated Corrective Action Plans to verify adherence to our Supplier Code of Conduct as well as training.
Associates who influence decisions in our supply chain are required to take training focused on modern slavery risks to heighten associates’ awareness and better enable them to recognize warning signs and know what tools are available to report concerns about forced labor or human trafficking. The training was developed in alignment with the International Labour Organization’s Indicators of Forced Labor. All associates involved in the production and purchasing process must understand the critical role they play. We are committed to providing these associates with ongoing training and educational opportunities to keep teams vigilant and fully engaged. The training reinforces our standards and expectations as set forth in our Code of Conduct and Supplier Code of Conduct.
Optimizing Our Supply Chain
Powered by agility and innovation, our predominantly U.S.-based supply chain enables us to deliver high-quality, on-trend luxuries at affordable prices. In recent years, we have moved more production to North America, our largest market, to not only improve supply reliability, but also provide speed and agility to our business and help to reduce our supply chain’s carbon footprint.
Our strategic vendor relationships provide deep capabilities across our product categories. Our supply base includes long-standing vendor relationships with the majority of our products being produced at Beauty Park, a business park in close proximity to our central Ohio home office/distribution and fulfillment centers.
Our company-owned distribution and fulfillment centers located in central Ohio are core to our operations. We also use third-party distribution centers, third-party-operated direct channel fulfillment centers and pop-up fulfillment facilities as needed, located throughout North America, to better position inventory geographically.
For non-merchandise materials, including those used for store design and construction and design and development, we maintain close business relationships with our production partners both domestically and overseas. Our partners provide high quality, speed and reliability, and most of them are local to our business needs.
Product and Sourcing Risk Council
Our Product and Sourcing Risk Council, composed of cross-functional senior executives, meets quarterly to discuss core business, sourcing and purchasing practices, review sustainability risks and opportunities and review and update, as needed, supply chain policies.
What We Expect from Suppliers
We insist that our suppliers comply both with the laws and regulations that govern their businesses and our company’s compliance standards and policies. If we discover that a supplier or factory is not in compliance, we partner with them to bring them into compliance. We are committed to continuous improvement and will not partner with suppliers and factories that are unwilling or unable to achieve compliance.
Suppliers sign a Master Sourcing Agreement (MSA) before we issue purchase orders and production commences. The MSA states that suppliers must comply with our policies and all applicable laws and regulations. The Bath & Body Works supplier Compliance Guidebook contains the policies with which our suppliers and their factories, suppliers and subcontractors must comply.
The Bath & Body Works Supplier Code of Conduct sets forth standards, in addition to all relevant laws, regulations and conventions, that apply to suppliers and their factories, sub-suppliers and subcontractors. Suppliers must adhere to these standards and communicate them to all workers in all countries where they operate. The Supplier Code of Conduct is based on core ILO Conventions, the Universal Declaration of Human Rights and Principles 1-6 of the UN Global Contract.
The vast majority of Bath & Body Works products are produced in the U.S., but when we do source products and components in other countries, we leverage our Trade Compliance Program.
For items imported, Bath & Body Works makes sure to accurately report the country of origin and place of manufacture to U.S. Customs and Border Protection (CBP) for each purchase order. To help ensure accuracy, we verify the factory is capable of making the products at issue, noting the appropriate manufacturers on commercial shipment documents, and that they did not subcontract orders without our explicit approval.
Further, the Trade Compliance Program assesses a factory’s ability to provide complete and accurate documentation to support a product’s country of origin and place of manufacture upon request from CBP. Bath & Body Works will assess each factory’s production process and capacity by observing the factory set up as well as inventory, production and shipment records.
Suppliers must require each of its factories that manufacture all or any part of Bath & Body Works goods to maintain production documentation for a period of at least two years (or longer if specified by Bath & Body Works) following the shipment of goods. Such records are necessary to establish the origin of all goods produced and to satisfy other regulatory requirements that may rely on manufacturing records.
Factories are expected to provide evidence of raw materials sourced and received prior to production. Factories must maintain production records for each process performed at a factory and commercial shipment documentation reflecting the correct factory name and address.
Bath & Body Works or our approved third-party auditor has the right to require a supplier or its factories to permit access to any and all records required to conduct origin verifications or capacity monitoring. Such records must be maintained in a form and at locations that will allow prompt review by the auditor.
In addition to monitoring labor standards and workplace conditions for all factories, we conduct trade assessment audits that enable us to identify any instance where unauthorized subcontracting has taken place at our factories. Unauthorized subcontracting is considered a major violation; therefore, we heavily monitor each factory to ensure all production is taking place at the factory named on the purchase order. We continue to emphasize our intolerance of unauthorized subcontracting in our annual training with suppliers and factories as well as highlighting it in the Compliance Guidebook.
The Bath & Body Works Supplier Code of Conduct clearly states that prison, indentured, bonded, involuntary or slave labor or labor obtained through human trafficking shall not be used. Forced, prison, indentured, bonded and slave labor, as well as labor obtained through human trafficking, are prohibited throughout our supply chain. Employers must not require workers to provide deposits or recruitment fees. If recruitment fees exist, the employer is responsible for payment of all employment eligibility and recruitment fees. The employer is not entitled to retain workers’ personal identity documents and all workers must have freedom of movement. Read our Transparency in the Supply Chain Policy.
Experts report that foreign migrant workers who travel across country borders to obtain employment are most at risk for human trafficking and forced labor, and therefore, we have established a Foreign Migrant Worker Policy to ensure that we reduce the risk of human trafficking or forced labor within our supply chain. In order to use a factory that employs foreign migrant workers, the sourcing team must obtain executive approval which can only be given if the factory receives positive results on a specialized audit developed in accordance with the International Labour Organization’s handbook on Combating Forced Labour. Factories that employ foreign migrant workers are closely monitored to ensure there are no forced labor violations and that workers have freedom of movement and are treated in accordance with the law. Any associate who contracts a factory that uses foreign migrant workers without executive review and approval is subject to disciplinary action, including, but not limited to, termination of employment.
The U.S. Securities and Exchange Commission (SEC) rule for disclosing conflict minerals requires public companies to make certain disclosure related to their use of “conflict minerals,” such as tin, tantalum, tungsten and gold (3TG), from the Democratic Republic of the Congo and adjoining countries (DRC+9), where violence and human rights abuses by armed groups have occurred in connection with the extraction of the minerals. Governments, NGOs, investors, customers and other industry stakeholders have increasing expectations to drive responsible behavior deep into companies’ supply chains.
We prohibit our suppliers from using conflict minerals.
To support compliance with the SEC’s rule, we require our suppliers to do the following:
Agree to avoid sourcing any 3TG which may directly or indirectly finance or benefit armed groups in the DRC+9.
Gather information from their supply chains regarding the origin of 3TG in their products, including the names and locations of smelters or refiners, and disclose that information in a timely manner to Bath & Body Works upon receipt of a request. Bath & Body Works makes this request annually.
Contact Bath & Body Works if they find any 3TG in their products that originated in the DRC+9.
Retain records related to their 3TG supply chain inquiries for a minimum of five years and make them available to Bath & Body Works or its designee during audits or upon request. This includes declarations from sub-suppliers, purchasing records, etc.
We are a member of the Responsible Mineral Initiative (RMI), an industry group that exists to assist member companies to investigate and mitigate risks associated with the use of conflict minerals in their products. We use RMI’s resources to compare the smelters and refiners (SORs) reported by our suppliers to the publicly available list of known SORs, to ensure that our suppliers are conformant with our policy.
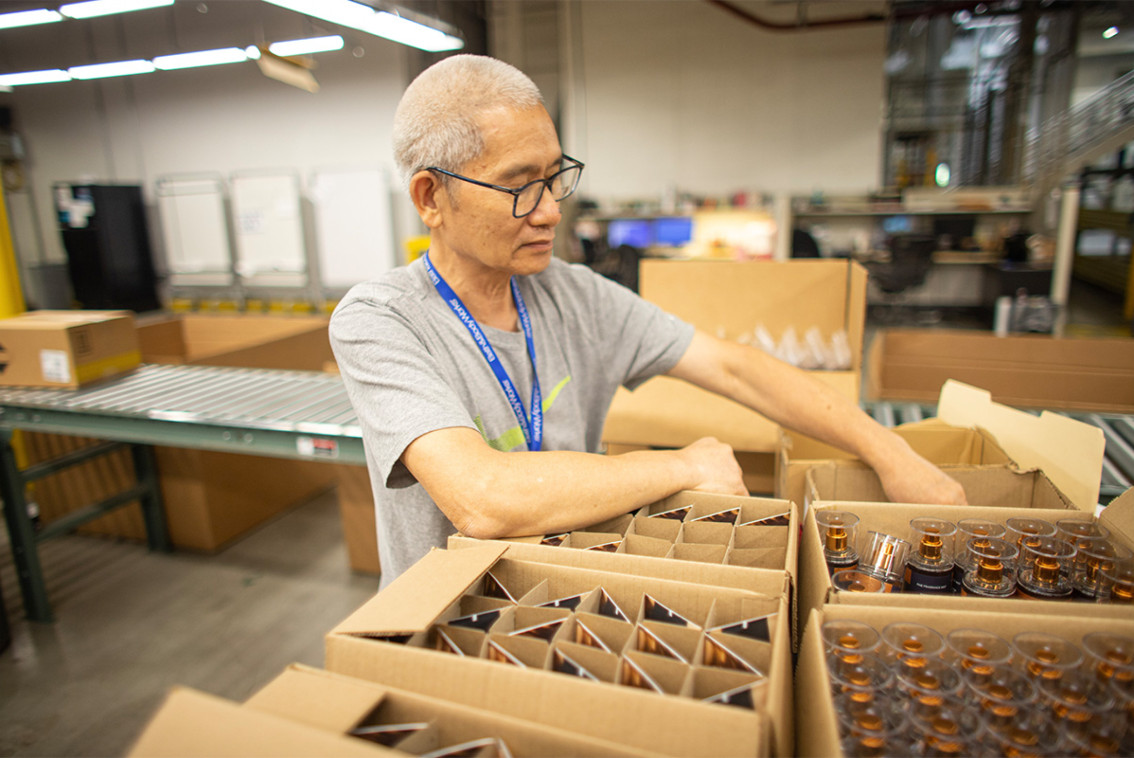
Environmental Impact
We've made several changes to reduce the environmental impact of merchandise and non-merchandise materials, including where and how they are sourced.
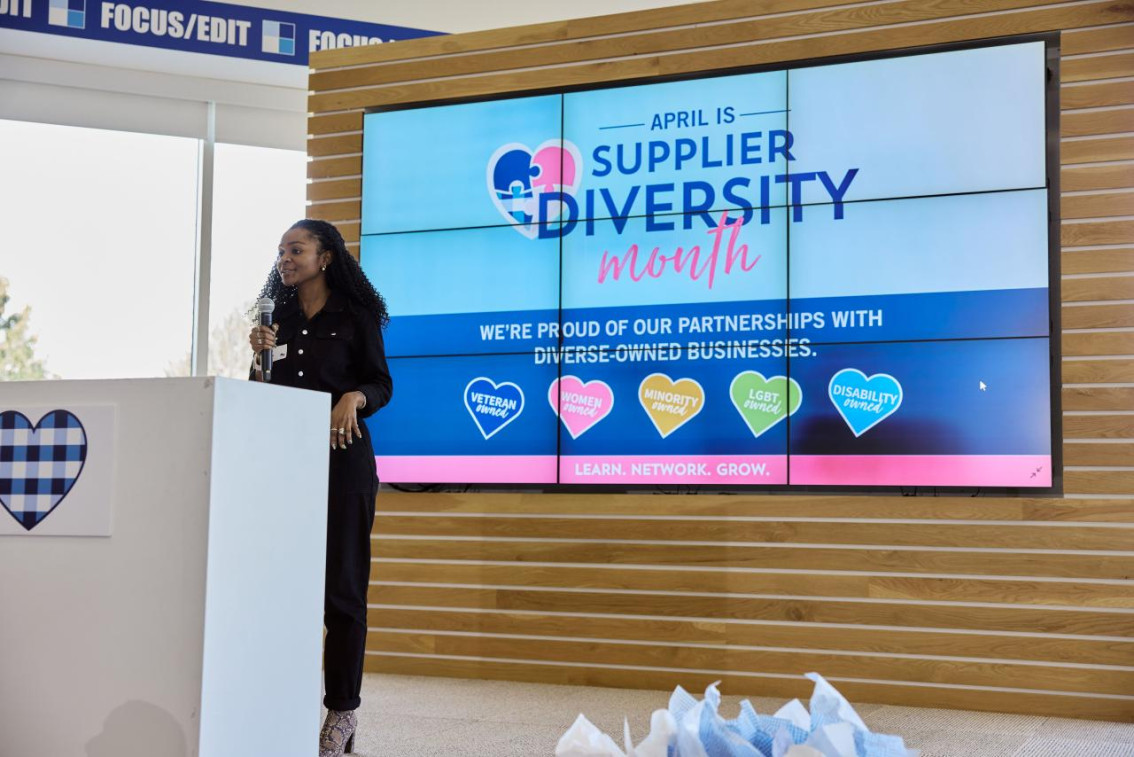